Spirometer
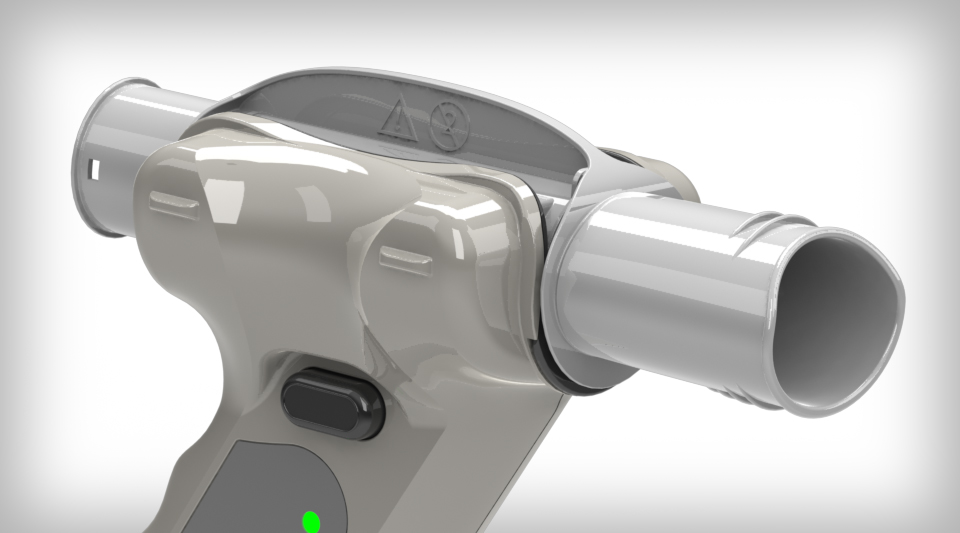
The Challenge
A medical company wanted to develop a lung capacity measuring device (spirometer) that had distinguishing user features and also fit with their established customer base. Their existing products are used in industrial and manufacturing environments and on military bases. However, the spirometer needed to look and function like a modern medical product and also be able to transition into general health care in the future for expanded sales.
The spirometer needed to look and function like a modern medical product and also be able to transition into general health care in the future for expanded sales.
The airway tube that the patient blows into is a single use part. Once a patient blows into the mouth piece it is undesirable for the examiner to touch it. The customer wanted a no-touch way to dispose of the airway.
The airway also offered unique design challenges. To measure lung capacity, sonic energy travels transversely through the tube from an emitter to a detector. This required the airway to have a hole in each side. The base handle needed to be kept clean for many uses. Therefore, the openings in the airway needed to have a very fine nylon screen captured around the perimeter to keep any mate-rial from exiting the side openings in the airway tube.
The Solution
An attractive and ergonomically shaped product case was created that provided a handle area where the patient held the device when they were using it. This was then taken into full product design and a PCB outline generated and placement of components that interact with the plastic case defined. The sonic transducers were mounted at an angle to the airway tube to provide a maxi-mum distance possible to make the most accurate measurement of airflow.
The issue of not touching the airway after the measurement procedure was solved by designing a system that involved a spring loaded ejector and release button. This system allowed the health care technician to take the device from the patient, walk over to a waste bin, and eject the used airway without having to touch it. In an environment of ever increasing drug resistant bacteria, this feature offered a competitive advantage.
To capture the airway opening screens, a low volume production technique was developed that used sonic welding energy to melt / weld the screen piece to the side of the airway. In high volume the screens will most likely be insert-molded into the airway tube. The sonic welding technique was an effective bridge manufacturing technique that allowed a sizable number of airways to be manufactured until the expensive production tooling could be brought on-line.